Advanced Techniques in Standing Seam Zinc Cladding
- Anna Wrench
- Jul 7
- 5 min read
Have you ever wondered why zinc cladding is the same for state Art Architectural projects throughout Australia? What does this versatile content do this versatile in the sea of traditional alternatives? And perhaps the most important thing is how to use the full potential to build buildings that are both fantastic and durable?
The standing seam represents an ideal marriage to zinc cladding form and function and offers architects and builders a material that is practical. From the prestigious cultural centres of Melbourne to the smooth commercial development in Sydney, the specific beauty and extraordinary performance characteristics of standing seam zinc cladding have made it a rapidly popular alternative. But here is the case while the zinc cover can look straight on the surface, its advanced installation techniques and design options require a deeper understanding of masting him.

Understanding Advanced Installation Techniques
When it comes to zinc cladding, the difference between an average status installation and excellent work is often contained in used techniques. Let's start with pre-Uholy methods, where the revolution has come up with how we contact zinc aesthetics. Natural cutting occurs when zinc reacts with atmospheric elements over time, requiring gray lenna. However, it is not always convenient to wait for this process.
Thermal movement calculations might sound like something from an engineering textbook, but they're vital for zinc cladding success. Zinc expands and contracts significantly with temperature changes – we're talking about movements of up to 2.2mm per metre with a 100°C temperature swing. Smart joint design accommodates this movement through carefully calculated expansion joints and clip spacing.
Complex Roof Geometries and Custom Solutions
Modern architecture is rarely resident of simple rectangles, and zinc cladding has evolved to meet these creative challenges. The curved and tailed seams provide remarkable flexibility in zinc. Through careful planning and special formation techniques, zinc can follow the complex decline while maintaining weathering. The secret panels and strategic seams are in progressive taping of placements.
Integration with solar panel systems presents unique challenges and opportunities. The key is planning from the outset retrofitting solar onto existing zinc roofs often compromises both systems. Modern solutions include integrated mounting rails that clip directly to standing seams, eliminating roof penetrations.
Performance Enhancement Strategies
Getting the most out of the zinc cladding installation is beyond the safety of the basic season. Ventilation requirements vary greatly in different climatic regions in Australia. In tropical regions, aggressive ventilation prevents moisture that can cause premature rust. On the other hand, in the dryer, ventilation mainly controls thermal stress. At least 40 mm ventilation cavity works for most applications, but coastal or high hungry areas benefit from increased airflow.
Acoustic performance is often ignored in cladding specifications, but zinc provides fantastic sound-numbers. The density of the material naturally reflects the sound, but the smart design increases these benefits. Inclusion of acoustic insulation in the ventilation cavity makes the cladding an effective noise barrier. Perforated lining trays with support materials form a sophisticated acoustic system suitable for airports, schools and other noise -sensitive applications.
Innovative Jointing and Seaming Methods
Double lock seams provide better weather resistance and structural ability, making them ideal for low -picked roofs and extreme weather risk. Mechanical folding creates an incredibly strong connection that can withstand significant wind raising. Single seams, although a little less strong, provide a cleaner look and sharp installation. They work brilliantly for vertical applications and statement where water apology is less important.
Expansion joint placement requires careful consideration of both technical requirements and visual impact. The general rule suggests expansion joints every 10-15 metres, but this varies with temperature ranges and panel dimensions. Strategic placement can enhance architectural expression – using expansion joints to define building modules or highlight entrances.
Troubleshooting Common Installation Challenges
Even experienced installers encounter challenges with zinc cladding but knowing how to address them makes all the difference. Irregularities in the substrate are one of the most common problems. Unlike some cladding materials, which can withstand errors, the smooth surface throws on zinc light on each shock and hollow. The solution begins with strict substrate inspection and preparation. Using a straight edge to check for deviations, shimming where necessary, and potentially installing a corrective layer can save hours of frustration later. For existing buildings, laser scanning technology now allows precise mapping of substrate conditions before cladding design begins.
Managing complex penetrations and services requires forward thinking and close coordination with other trades. Each entry through zinc cladding represents a possible leakage point, so it makes sense to minimize them. When the entry is inevitable, shiny designs are important.
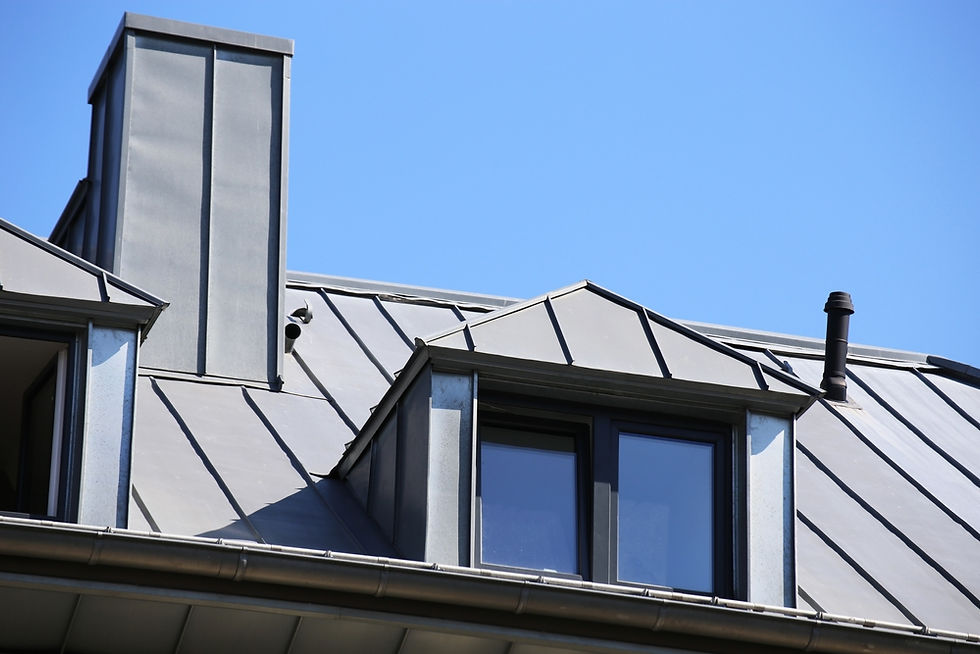
Cost-Effective Design Strategies
Optimising panel widths for material efficiency starts with understanding standard coil widths and working backwards. Most zinc comes in 1000mm coils, so designing panels that efficiently use this width reduces waste. Consider how seam spacing affects both material usage and labour costs. Wider panels mean fewer seams to form but might require additional stiffening.
Value engineering for zinc cladding shouldn't mean cutting corners. Instead, focus on design decisions that simplify installation while maintaining performance. Standardizing panel lengths where possible reduces fabrication complexity. Minimising custom flashings through clever design saves both material and labour costs.
Maintenance and Longevity Best Practices
Active maintenance transforms good zinc installations into extraordinary people who have been for previous generations. The inspection program shall correspond to building use and environmental risk. For most applications, annual visual inspections are sufficient, with detailed inspection every five years. Coastal or industrial environment benefits from six-mask checks. Make the seam, flashing, fixed and drainage paths covering checklists. Documents conclusions to track changes over time.
Cleaning methods vary with zinc finishes and soiling types. Natural and pre-weathered zinc generally require minimal cleaning often just rainfall suffices. For stubborn spots, special zinc cleaners work without damaging petina. Always test the methods of cleaning in the first incompatible areas.
Future Trends and Sustainable Innovations
The zinc cladding industry continues, inspired by stability requirements and technological development. Recycled zinc materials continue to grow, with some manufacturers now offer products with more than 40% recycled materials. This circular economy reduces the environmental impact by maintaining approach standards. Recycling in End-Off-Life reaches 100%, making zinc one of the most permanent cladding options. As environmental product declarations become standard, zinc's credentials shine even brighter.
Integration with green building rating systems has become seamless, with zinc contributing to multiple credit categories. Beyond obvious materials credits, zinc supports energy efficiency, indoor environmental quality, and innovation categories. Smart building technology compatibility opens new possibilities imagine zinc cladding with integrated sensors monitoring building performance or LED systems creating dynamic facades.
Conclusion
Standing seam zinc cladding represents far more than just another cladding option It is a refined building system that combines beauty experience with excellent performance. During this discovery of advanced techniques, we have seen that proper understanding and application of these methods can increase projects from simple to extraordinary.
Looking ahead looks the future of zinc cladding brighter than ever. With the promotion of technology, increasing stability awareness and increasing praise for quality materials, zinc is ready to meet tomorrow's building challenges. By embracing these advanced techniques and creating a commitment to crafts, we can build motivated buildings today while we are strong for generations to come.
Comentarios