Customizable Coalescing Plate Oil Water Separators for Commercial Sites
- ameliya lanne
- Jun 16
- 13 min read
Have you ever wondered how commercial sites manage large volumes of oily wastewater? Are you curious about the difference between a standard oil water separator and a coalescing plate oil water separator? Perhaps you’re keen to learn why Australian regulations are so strict when it comes to industrial water treatment. In this post, we’ll tackle these questions head-on with a friendly, straightforward approach.
We’ll explore the fundamentals of oil water coalescer technology and uncover why customisable coalescing plate oil water separators are so important for commercial applications. You’ll discover how these systems help businesses stay compliant with Australian regulations while keeping operational costs in check. Plus, we’ll discuss everything from design options to maintenance routines, ensuring practical tips for anyone looking to upgrade or install a new separator system.
By the end, you’ll have a thorough understanding of how coalescing filter oil water separators work and why they’re the go-to method for handling oily wastewater. You’ll come away with insights on portable oil separator units, recommended cleaning schedules, and even region-specific advice if you’re considering an oil water separator in Perth. Ready to dive in? Let’s get started.

Overview of Oil Water Separation Basics
Oil water separation is a fundamental process used in many commercial and industrial settings. It’s crucial because raw oily wastewater can wreak havoc on local ecosystems if released untreated. Leftover hydrocarbons might also damage plumbing and sewerage systems, leading to expensive repairs or fines. To prevent these issues, businesses implement separators that pull oil and other contaminants out of water before discharge or reuse.
A basic oil water separator relies on the principle that oil is lighter than water. When given enough time in a settling tank, oil droplets float to the surface, where they can be removed. However, in high-volume or heavily polluted situations, traditional separators may not be enough. That’s where a coalescing plate separator steps in. It features specialised coalescing plates designed to gather and merge smaller oil droplets, making it much simpler to skim them off. This technology greatly speeds up the separation process and boosts overall system performance.
Thanks to Australia’s environmental regulations, many commercial sites must invest in advanced separation methods. A coalescing plate oil water separator fits the bill for most industries, as it’s both effective and adaptable. By understanding these basics, you set the stage for exploring the many ways coalescer oil water separators help commercial operations run more smoothly.
Importance of Customisable Coalescing Plate Oil Water Separators
When it comes to managing oily wastewater, one size doesn’t fit all. Different industries face unique challenges, whether it’s a high flow rate, unusual contaminants, or limited floor space. By opting for a customisable coalescing oil separator, you gain the flexibility to adjust the system's capacity, materials, and overall design. This ensures you’re not stuck with an off-the-shelf product that falls short when conditions change.
Tailor-made coalescing plate oil water separators also help businesses comply with local regulations more easily. If you operate in Australia, you know the rules can vary from one region to another. Designing a separator that aligns with specific guidelines from the get-go can spare you unnecessary headaches down the line. Additionally, a customised solution often leads to improved efficiency because it matches your requirements—from handling heavy oil loads to dealing with chemical emulsions.
Finally, the ability to modify your coalescing plate interceptor or oil coalescer water oil separator can futureproof your operations. If your production levels rise, it’s much simpler to scale up an existing design than install a completely different system. This adaptability, coupled with reliable results, helps businesses save money while meeting environmental targets. It’s a win–win scenario for both companies and the planet.
Why Commercial Sites Need Coalescer Oil Water Separators
Commercial facilities often generate large volumes of wastewater laced with oil, solvents, and other pollutants. Car parks, workshops, and manufacturing plants are just a few examples of places where oily runoff may become a pressing concern. Installing a coalescer oil water separator ensures efficient removal of these contaminants, protecting local waterways and helping you avoid substantial fines.
Beyond avoiding regulatory fines, a coalescing plate separator can dramatically reduce maintenance demands on sewerage infrastructure. When oily waste isn’t handled properly, it can build up in pipes and pumps, leading to clogs or costly breakdowns. Additionally, removing oil at the source helps recycle water for reuse in certain processes, cutting down on overall consumption and lowering operational costs.
Investing in an oil coalescer water oil separator also supports environmental stewardship. No company wants to be associated with pollution incidents, and adopting the right technology sends a strong message about corporate responsibility. Moreover, proactive management of wastewater paves the way for smoother expansions in the future, as you’ll already have the infrastructure to handle higher volumes.
Common Environmental and Regulatory Challenges in Australia
Australia enforces strict environmental guidelines due to its sensitive marine and land ecosystems. Commercial sites that fail to comply risk not only hefty penalties but also potential damage to their reputation. Regulations typically mandate that effluent leaving a facility must meet specific oil concentration limits before being released.
Additionally, water usage can be costly, especially in regions facing frequent droughts. Minimising water waste isn’t just an eco-friendly choice; it also has a direct impact on your bottom line. Coalescer oil water separators make it easier to recycle water, cutting down on usage fees and meeting local requirements for wastewater management.
How an Oil Coalescer Water Oil Separator Helps Mitigate Risks
A coalescer oil water separator effectively traps and coalesces oil droplets to prevent them spreading into the environment. By accelerating the merging of tiny droplets into larger ones, it makes removal swift and consistent. This not only keeps your facility in compliance but also lowers your chances of facing clean-up costs or reputational damage from accidental spills.
Moreover, these separators can handle varying flow rates, ensuring that unexpected surges in runoff don’t compromise water quality. In situations where multiple contaminants are present, advanced systems can be enhanced with additional features like filters or carbon beds to tackle different pollutants. The result is a comprehensive approach that helps manage both regulatory and operational risks in one fell swoop.
Understanding Coalescing Plate Oil Water Separator Technology
Coalescing plate oil water separator are built to handle challenging wastewater conditions. They use coalescing plates to attract and combine oil droplets more efficiently than standard separators. The larger droplets then rise to the surface quickly, simplifying the skimming process. This makes coalescing filter oil water separators ideal for commercial operations with high flow rates or heavy oil loads.
Another benefit is their compactness. By using internal coalescing plates, these units can process large volumes of wastewater in a relatively small footprint. This advantage is especially helpful if you’re operating in an area where space is at a premium. Because of their adaptability, coalescing plate interceptors are popping up everywhere from vehicle maintenance centres to chemical manufacturing sites.
Understanding how they differ from other separators is essential for making an informed decision. While gravity-based systems work well for lighter oil concentrations, coalescing oil separators excel when facing more complex waste streams. The key is to identify which approach aligns best with the nature of your wastewater and your long-term objectives.
Key Components: Oil Separator Plates and Coalescing Plates
At the heart of a coalescing plate oil water separator are two types of plates: oil separator plates and coalescing plates. Oil separator plates are generally arranged to create a series of parallel channels through which water can flow. Their angle helps direct oil droplets upwards, improving separation efficiency.
Coalescing plates contain a special surface texture that encourages tiny oil droplets to gather together. As these droplets unite, they become large enough to rise swiftly to the surface. This design dramatically shortens the settling time, so you achieve high rates of oil removal in a compact unit. The synergy between oil separator plates and coalescing plates is what makes these systems stand out.
Coalescing Filter Oil Water Separators Work
Coalescing filter oil water separators rely on gravity, surface tension, and the coalescing effect. Wastewater enters the chamber, flowing through sets of parallel plates. Microscopic oil droplets adhere to the plate surfaces, merging into bigger droplets. These larger droplets detach and float upwards, forming an oil layer at the top.
Meanwhile, the cleaner water continues below, where any remaining particles can collect in a sludge zone at the bottom. Skimmers or pumps remove the separated oil layers, and sediment can be drained from the base. The overall process is straightforward yet highly efficient, making coalescing filter separators a favourite in industries that need consistent, reliable oil separation.
Coalescing Plate Interceptor vs. Other Oil Water Separator Types
Traditional oil water separators rely mainly on gravity to separate oil from water. While sufficient for light contamination, these systems often struggle with emulsified oils or heavier, more complex waste streams. A coalescing plate interceptor, on the other hand, actively accelerates droplet formation, allowing for quicker and more efficient removal.
Other technologies include dissolved air flotation systems, which use tiny bubbles to lift oil particles to the surface. While effective, such solutions can be more expensive and involve complex chemical treatments. Coalescing plate interceptors strike a balance by offering robust performance without the higher costs and complexities of more advanced separation gear.
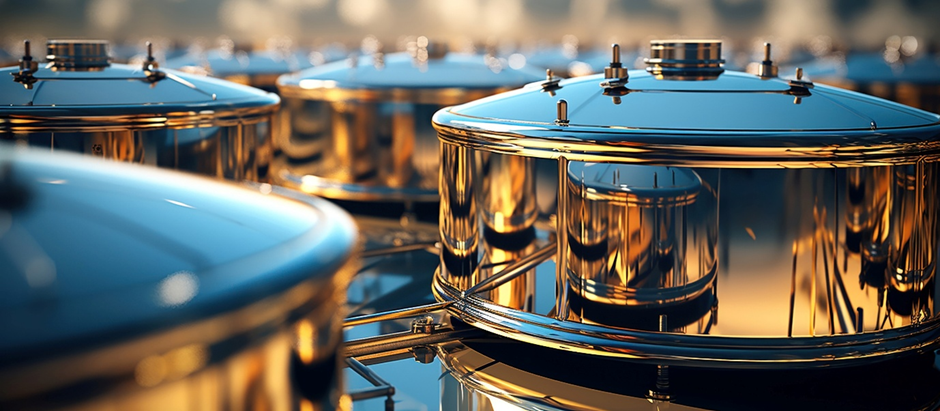
Design and Customisation Options
No two commercial operations are identical. Some might handle bulk oils daily, while others deal with sporadic sludge. That’s why a one-size-fits-all coalescing oil separator rarely matches real-world demands perfectly. Instead, many suppliers offer customisable features like adjustable flow capacity, specialised materials, and built-in filters for specific contaminants.
Moreover, operators can choose from various unit sizes and tank shapes. Do you have a tight underground space, or perhaps you require a skid-mounted system for easy relocation? You can discuss these practicalities with specialised suppliers to ensure the design suits your location. By investing in a custom approach, you maximise efficiency while ensuring compliance with local mandates.
Tailoring Coalescing Plate Separators for Specific Industries
Construction sites, automotive workshops, and food-processing plants each face different contaminants. A construction site might deal with grit and sediment, while a workshop oil water separator must manage lubricants and hydraulic fluids. By identifying these unique pollutants, you can add extra fittings like filtration media or pre-screens to your coalescing plate separator design.
Industries operating near protected habitats or sensitive wetlands may require additional safety features. Spill containment areas, remote monitoring systems, or automatic shut-off valves are examples of customisations. Such design tweaks help ensure that even the smallest leak is managed effectively, keeping your business on the right side of environmental regulations.
Selecting the Right Materials and Configurations
One of the most overlooked factors in picking a coalescing plate oil water separator is material selection. Stainless steel is popular for harsh industrial environments, thanks to its corrosion resistance and durability. Fibreglass or reinforced plastics might be chosen when cost or weight is a major concern. The specific configuration—whether rectangular, cylindrical, or modular—also plays a role in efficiency and maintenance.
Other design details, like inlet and outlet positioning, can significantly impact performance. For example, introducing wastewater at a particular angle could reduce turbulence, giving oil droplets more time to coalesce. In many cases, working with a technical specialist to tailor these small yet impactful details leads to a separator that operates reliably and requires minimal upkeep.
Workshop Oil Water Separator: Compact Solutions for Smaller Spaces
Workshop oil water separators work particularly well for garages, service stations, and small industrial units. Many such facilities have limited room for large-scale treatment plants. By incorporating coalescing plates in a compact tank, you can process wastewater quickly without sacrificing valuable floor space.
Another advantage is the relative ease of installation. These smaller units can often be placed above or below ground, depending on site constraints. With a workshop oil water separator, it becomes simpler to stay compliant—even if you’re running a small automotive business—without costly expansions or complicated infrastructure changes.
Portable Oil Separators: Flexibility for On-the-Go Operations
Sometimes, you need flexibility above all else. Portable oil separators fill that niche perfectly. They are designed to be moved from one job site to another, making them indispensable for contractors or maintenance crews working across multiple locations. Combine them with an oil separator pump, and you have a mobile, efficient system that manages oily wastewater wherever it appears.
Portable oil separators often come in skid-mounted or trolley-based configurations, allowing quick set-up and easy transport. Although smaller in capacity than permanent installations, they still use coalescing plates to offer efficient oil water separation. This flexible approach can be a game-changer for operations that cannot justify installing multiple fixed units at varying sites.
Installation and Maintenance Essentials
Even the best-designed coalescing plate oil water separator will falter without proper installation and ongoing maintenance. Whether you’re dealing with a small workshop oil water separator or a larger coalescing plate interceptor, careful planning is essential right from the start. This includes crafting solid foundations, aligning inlet and outlet pipes correctly, and selecting suitable pumps.
Once your system is up and running, regular inspection is key. This involves monitoring pressure drops, clearing blockages, and examining the coalescing plates for residue buildup. Consistent attention keeps performance high and reduces downtime caused by unscheduled repairs. Ultimately, giving these systems a bit of care ensures they meet both your capacity needs and local compliance standards.
Best Practices for Installing a Coalescing Oil Separator
Start by picking an installation spot with ample room for pipework, access hatches, and any additional filtration stages. In areas prone to flooding, it’s wise to reinforce or raise the separator to protect it from water damage. Also, consider adding gear like flow meters or pressure gauges so you can track performance in real time.
During the set-up process, verify that your inlet and outlet lines are placed at the recommended angles. Improper alignment can cause turbulence, reducing the efficiency of the oil water coalescer. It’s also beneficial to incorporate overflow alarms or automatic shut-off systems, giving you a safety net in case the unit approaches its maximum capacity unexpectedly.
Maintenance Schedules and Cleaning Techniques
Maintenance intervals will depend on factors like flow rate, type of contaminants, and local climate conditions. Heavy oil loads, for instance, will require more frequent cleanings. A common practice is to set up a quarterly inspection routine, where key elements such as skimmers, pumps, and coalescing plates are checked for wear and tear.
When cleaning coalescing plates, gentle methods are often best. Pressure washing can damage or dislodge delicate surfaces if you’re not cautious. Soaking plates in a mild cleaning solution helps dissolve residue without harming the material. Ensuring that sludge is properly removed and disposed of according to Australian regulations is also important for maintaining environmental compliance.
Maximising Efficiency with an Oil Separator Pump
An oil separator pump can be a true game-changer when it comes to smoothing out your wastewater management. By facilitating the transfer of oily water, these pumps keep flow rates stable and make sure any floating oil layers are promptly removed. This helps prevent the build-up of oils that might otherwise linger and contaminate outgoing water.
Moreover, a high-quality pump can reduce the manual labour involved in maintaining your coalescing plate separator. Instead of hauling out large quantities of oily sludge, you can rely on a pump to do the heavy lifting. This not only saves time but also minimises health and safety risks for employees tasked with handling potentially hazardous materials.
Pump Selection Criteria and Considerations
When choosing a pump for your coalescing oil separator, capacity and compatibility are crucial. The pump’s flow rate should match or exceed the expected peak flow of your system, ensuring water doesn’t back up. Materials matter too: for heavily contaminated water, corrosion-resistant components help extend the pump’s life.
Automatic level controls or timers can also improve the overall performance of your oily water treatment package. These features allow the pump to kick in only when needed, preventing continuous running and lowering power consumption. By carefully evaluating these aspects, you’ll end up with a pump that keeps everything running smoothly without overspending on energy or repairs.
Enhancing Flow Rate and System Performance
Adding a pump isn’t just about moving water; it can actively enhance how your coalescing plates function. A well-regulated flow ensures oil droplets have the right amount of contact time with coalescing surfaces. If the flow rate is too high, smaller oil droplets might slip through. If it’s too slow, the system might become stagnant, reducing efficiency.
Balancing the pump’s settings with the physical layout of your separator is where you can really optimise performance. For instance, adjusting inlet pressures, refining outlet positioning, or incorporating a surge tank helps regulate flow spikes. These small tweaks can lead to substantial improvements in oil removal efficiency over the long haul.
Choosing the Right Oily Water Treatment Package
These days, you can pick from a range of oily water treatment package solutions. Some come bundled with coalescing plates, pumps, and monitoring tools all in one neat offering. Others require you to assemble components from various suppliers, giving you more freedom but also more complexity. The right choice depends on your facility’s size, flow requirements, and budget.
One key question is whether you need advanced filtration phases beyond oil separation, such as active carbon or chemical treatments. While these can offer superior water purity, they also add cost and maintenance tasks. If you’re dealing with moderately polluted water, a well-designed coalescing plate oil water separator often hits that sweet spot where cost meets compliance.
Bundled Solutions vs. Standalone Options
Bundled solutions can be a great choice if you want a hassle-free installation. Everything you need is included in a single oily water treatment package, from the separator tank to the control systems. This can save time during installation and reduce the odds of compatibility hiccups between different components.
On the other hand, standalone options allow for more customisation. If you have a unique setup—like extreme temperature swings or multiple pollutant types—mixing and matching individual components can yield a highly targeted answer. While it demands more planning, the payoff is a system tailored to your facility’s exact conditions.
Balancing Cost, Compliance, and Capacity
When selecting your treatment package, keep an eye on three things: the system’s total cost, its ability to meet local regulations, and its capacity to handle future growth. While it might be tempting to go cheaper upfront, cutting corners often leads to steep maintenance bills and possible fines if you falter on compliance.
Likewise, over-investing in a top-of-the-line system that’s too big for your current needs might be a waste of resources. The ideal setup is one that provides reliable wastewater treatment for your typical flow rates, with a bit of room to grow if production accelerates. Striking that balance can make your facility more resilient and future-proof.
Oil Water Separator Perth: Regional Installation Insights
Perth’s climate and regional conditions can influence how you select and maintain a coalescing oil separator. Western Australia experiences long, hot summers, which can pressurise water resources. Companies might face stricter water usage guidelines, making efficient recycling a must. Fortunately, Perth also boasts a variety of experienced local suppliers who can customise solutions for the region’s needs.
When looking for an oil water separator in Perth specifically, you’ll want to ensure compliance with state-level regulations. Requirements for discharge and monitoring can vary, so having a local consultant can simplify the process. Moreover, choosing a nearby supplier can streamline maintenance and spare you shipping costs when replacing parts like coalescing plates or pumps.
Conclusion
Has this journey into coalescing plate oil water separators sparked new ideas for your commercial site? We’ve explored how these advanced units outdo standard gravity-based systems, especially when juggling high flow rates or stubborn oil contaminants. Best of all, they’re adaptable—tailored designs can be scaled up or streamlined to match the changing demands of your facility.
At their core, coalescing plate oil water separators offer a reliable way to safeguard both the environment and your bottom line. By coalescing oil droplets efficiently, they reduce the risk of non-compliance and preempt costly damage to infrastructure. They also pave the way for on-site water recycling, which can shrink your overall water usage and demonstrate corporate responsibility.
If you’re considering installing or upgrading your system, remember that the perfect fit involves more than just the separator itself. Think about local regulations, available space, planned expansions, and your budget. By factoring in these details from the outset, you’ll set yourself up for long-term success. Ultimately, investing in the right coalescer oil water separator is an investment in your future, ensuring smooth operations and peace of mind for years to come.
Comments