Have you ever wondered why so many new builds feature sleek grey exteriors? Are you curious about materials that stand the test of time, while also looking modern and chic? Perhaps you’ve noticed zinc cladding on a home or commercial building and thought, “What makes that stand out so much?”
By the end, you’ll have a thorough understanding of zinc cladding’s benefits, installation, and care. Plus, you’ll be ready to make confident decisions about your own project, whether it’s a cosy renovation or a large-scale commercial build. Let’s dive in and discover why zinc continues to be the go-to choice for architects and homeowners alike.
Understanding Zinc Cladding
What Is Zinc Cladding?
Zinc cladding is a protective layer made from sheets of zinc metal, which are installed on a building’s façade or roof. It’s widely used because zinc is both lightweight and durable, making it an appealing alternative to heavier metals. Many architects love how zinc adds a sleek, contemporary look to projects.
Unlike traditional finishes, zinc also forms a natural patina over time, allowing it to repair minor scratches on its own. This patina develops when zinc reacts with the air and rain, creating a surface layer that shields the metal underneath. As a result, zinc cladding often looks better as it ages.
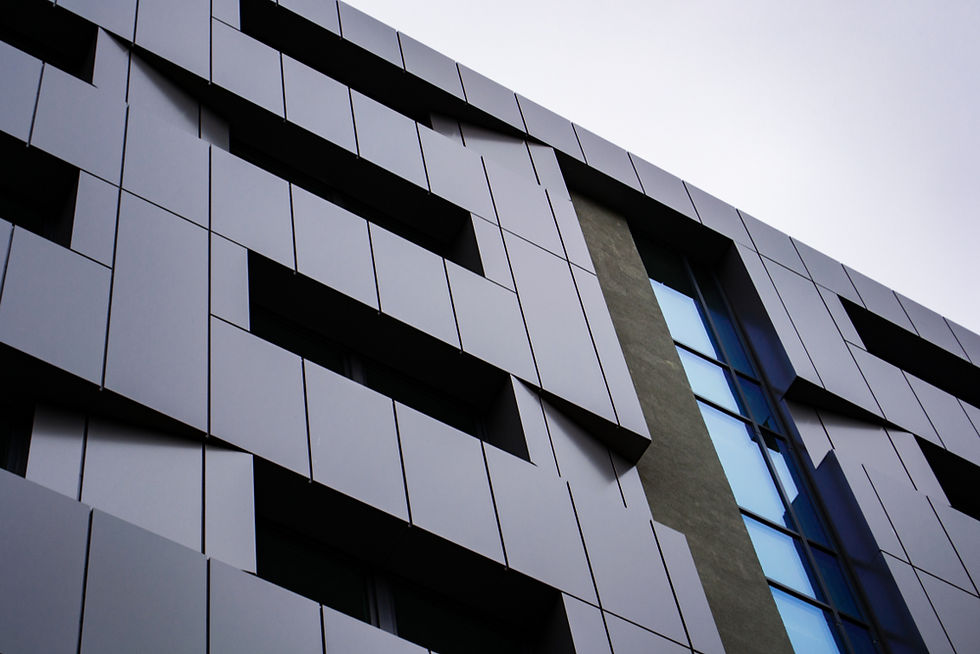
Key Benefits of Using Zinc
One major advantage of zinc cladding is its impressive longevity. This material is known for lasting several decades, even under harsh weather conditions. Another benefit is how easy it is to mould and shape. This flexibility offers unique design opportunities, giving architects the freedom to create eye-catching curves and angles.
Zinc is also relatively low-maintenance compared to other cladding materials. Its patina layer helps it resist rust and corrosion, making it ideal for buildings in coastal regions or areas with unpredictable weather patterns. Furthermore, zinc is considered recyclable, which is always a plus for anyone keen on eco-friendly construction solutions.
Types of Zinc Cladding Systems
Zinc cladding comes in a range of styles, each suiting different project needs. Here’s a quick overview of some popular systems that you may come across when exploring your options.
Standing Seam
Standing seam zinc cladding involves long vertical or horizontal panels with raised seams where the sheets join. These seams give a distinct texture to the building’s exterior while ensuring a watertight seal. Because zinc is so flexible, it’s easier to install standing seam panels on curved or angled surfaces, making it a top choice for architects pursuing a modern, fluid look.
Interlocking Panels
Interlocking panels are designed to “click” together along neatly concealed joints. This approach is fantastic for achieving a crisp, uniform façade with minimal fuss. These panels are customisable in size and shape, providing varied design possibilities. Builders also favour interlocking panels for their quick, efficient installation process.
Flat-Lock Panels
Flat-lock panels are installed with overlapping edges, creating a tight fit that looks almost seamless from a distance. They offer a more understated aesthetic compared to standing seam systems, yet still provide excellent weather resistance. These panels can be arranged in horizontal or vertical layouts, giving designers lots of freedom to experiment with patterns.
Range of Finishes and Textures
Zinc cladding is not just limited to the classic grey patina. It’s available in various finishes, from smooth polished surfaces to textured or pre-weathered options that replicate the look of an aged patina straight out of the box. These choices let you match your cladding to the overall style of your building whether you prefer striking modern lines or a more rustic finish.
The Installation Process
Planning and Prep Work
A successful zinc cladding project begins with careful planning. Start by assessing the structure of your building, identifying any repairs that need to be addressed before installing metal sheets. Next, measure your façades or roof accurately so you can order the correct amount of zinc.
You’ll also need to decide on the cladding system such as standing seam or interlocking panels. Each method may have unique requirements in terms of sheathing, insulation, and fasteners. Getting all these elements right in the prep phase helps you avoid hiccups further down the line.
DIY vs. Professional Installation
Zinc is relatively easy to shape, but the mastery lies in ensuring secure seams and proper ventilation underneath the panels. For smaller or simpler projects, capable DIYers might take on the challenge themselves. However, if your project features complex shapes, or if you want optimal weatherproofing, an experienced installer is often the best route.
Timeline and Budget Considerations
The installation time frame depends on your project size and the complexity of your design. Standing seam systems typically take longer than interlocking panels due to the formed seams. Budget-wise, plan not only for the zinc sheets and labour but also for accessories like fixings, ventilation materials, and scaffolding if needed. A well-thought-out timeline and budget ensure fewer surprises along the way.
Maintenance and Care
Routine Inspections
Zinc cladding’s patina makes it impressively resistant to wear, but regular checks help catch small issues before they become big problems. Look for signs of damage, especially after wild storms or heavy rain. Check seams and flashing to confirm everything remains watertight.
Cleaning and Repairs
Cleaning is usually a breeze. A light rinse with water once or twice a year removes dirt or pollutants. If something more stubborn has built up, gentle wiping with a non-abrasive cloth may do the trick. For repairs, consult a professional if you notice deeper dents or seam separations, as proper techniques are needed to maintain a watertight seal.
Prolonging the Lifespan of Zinc Cladding
Good insulation and adequate ventilation behind the cladding are essential for minimising moisture buildup. Installing a high-quality breathable membrane ensures that any trapped water can exit, preventing issues like mould or corrosion. Additionally, regular checks on gutters and downpipes mean water flows away cleanly, reducing the burden on your cladding.
Comparing Zinc with Other Cladding Materials
Zinc is a popular choice, but how does it compare to alternatives like aluminium, timber, and steel? Understanding the differences helps you decide what best suits your project’s budget and design goals.
Zinc vs. Aluminium
Aluminium is lightweight, easy to install, and less expensive than zinc. However, it can lack the self-repairing patina and might need more regular cleaning to maintain a pristine look. Zinc, on the other hand, tends to look classy and refined over time.
Zinc vs. Timber
Timber brings natural warmth to a building’s exterior, but it often requires frequent re-sealing or painting to stay in good shape. While zinc may not achieve the same earthy charm, it delivers far lower maintenance and a longer lifespan in harsh conditions.
Zinc vs. Steel
Steel is strong and can be cost-effective, but it often requires galvanizing or paint to guard against rust—especially near coastal environments. Zinc’s inherent corrosion resistance can make it a less demanding choice in corrosive areas. In addition, zinc typically weighs less than steel, which may reduce structural demands.
Troubleshooting Common Issues
Addressing Corrosion Concerns
While zinc is highly resistant to rust and corrosion, it’s not invincible. In areas with high pollution or near industrial zones, the patina may develop faster. Occasionally, you might detect white streaks on the surface known as “zinc run-off,” particularly if the cladding is installed above porous materials. In many cases, proper drainage and the right flashing design minimise these stains and keep the surface looking great.
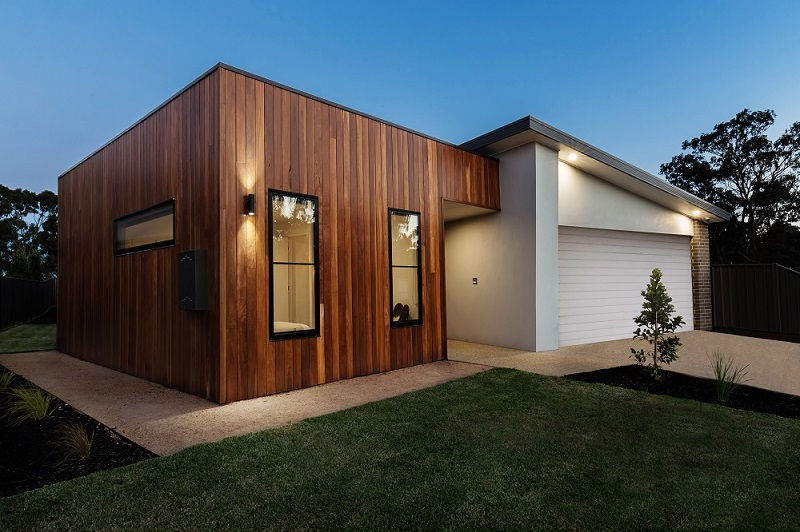
Identifying and Fixing Leaks
If you spot interior damp patches, it might indicate an issue with the cladding’s seams or flashing around edges. A professional inspection can locate the root of the leak. Replacing any damaged sections promptly can save you from more serious structural damage.
Ensuring Proper Insulation
If you experience unexpected temperature fluctuations or condensation inside your building, there might be a gap in the insulation behind the zinc. Sealing these areas or adding insulation in critical spots prevents moisture buildups and improves the energy efficiency of your property.
Choosing the Right Zinc Cladding Supplier
Quality and Reliability Checks
Not all zinc cladding is made equal. Some manufacturers specialise in premium zinc alloys, while others may cut corners. Always read product descriptions carefully to see if the zinc meets Australian construction standards. You can also ask potential suppliers about their sourcing and quality control measures.
Comparing Quotes and Services
Gathering multiple quotes is wise for spotting any large price discrepancies. Look not just at the cost but also at the services and warranties on offer. Some suppliers include brief consultations or pre-installation advice in their package, which can save you time and money.
Warranties and Guarantees
A company that stands behind its product is generally more trustworthy. Look for warranties that cover manufacturing defects and possibly even installation errors if they provide fitting services. The length and specifics of these guarantees can give you peace of mind that your investment is protected.
Conclusion
Now that you’re armed with knowledge, you’re ready to take the next steps. Whether you’re dreaming of a modern home façade or upgrading a commercial property, zinc cladding offers a premium balance of style and resilience. Start by obtaining quotes, gather design ideas, and speak with experts about local regulations. Soon enough, you could be admiring the sleek, long-running metal cladding that has taken your building to the next level.
Comments